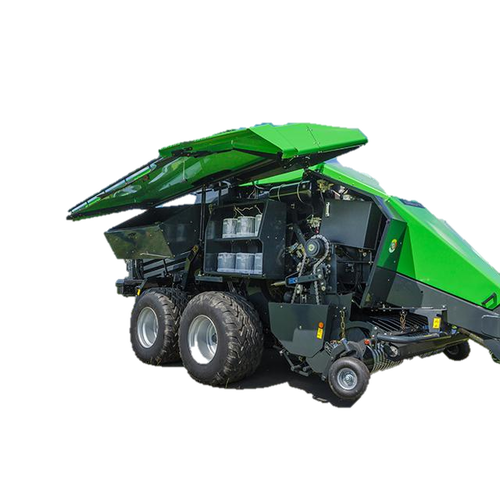
Big Balers
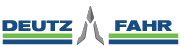
ULTIMATE FIELD PERFORMANCE, MAXIMUM OUTPUT
Our goal is to develop machines that will give a boost to the profitability of your company. High output is a key success factor for every large square baler. DEUTZ-FAHR BigMaster baling presses feature several unique points that will provide the capacity your company requires. The ability to produce top quality bales in all crop conditions sets DEUTZ-FAHR BigMaster baling presses apart from all the others. Perfectly shaped bales, high output and outstanding durability, ensure the DEUTZ-FAHR BigMaster will be a profitable investment. Pick-up: Featuring an innovative design, this pick-up, which measures 2.10 or 2.30 m, gathers even the thickest, tallest windrows effectively and quickly. The gradient control and height adjustment systems mean that the machine closely follows the contours of the terrain to ensure thorough gathering. The pick-up roller feeds material to the rotor effectively regardless of the conditions of the crop. Integral rotor: All DEUTZ-FAHR BigMaster balers, cutting or non-cutting versions are equipped with the INTEGRAL ROTOR. This simple, maintenance-free integrated rotor situated immediately behind the pick-up ensures the uniform feed of material to the press irrespective of the type of forage. The large inlet chamber prevents the risk of overload for superior performance in the field. The rotor also ensures that material is fed continuously to the compression chamber even when working with uneven windrows. OptiFeed and Biomass OptiFeed – Non cutting versions: The OptiFeed rotor design, where rotor tines - made out of Hardox® wear plate - and auger function are combined on one shaft, helps even out the swath by spreading the crop evenly for consistent bales every time. When crop cutting is not required, the OptiFeed system ensures a controlled and consistent crop flow to the pre-chamber. With the rotor, an additional level of protection is added to the machine. The 60 cm diameter Biomass OptiFeed rotor design combines all the benefits of the standard OptiFeed rotor with boltable rotor tines made out of Hardox® wear plate for excellent durability and easy exchange. These rotor tines are specially designed for aggressive energy crops such as sugar cane leaves. OC – Cutting versions: The OC cutting systems are designed for unlimited intake capacity. There are three different types of OC cutting system (availability dependent on BigMaster model): OC 15: The OC 15 offers a cutting length of 45 mm. The patented rotor tine shape ensures a low power requirement and a perfect cutting quality. The knives, individually protected with a spring, can be changed easily with the standard cassette system. OC 23: The OC 23 offers a cutting length of 45 mm on the 120 cm wide channel models. With a rotor diameter of 60 cm, the OmniCut rotor will process every swath that is placed in front of the baler. The knives on the OC 23 have individual hydraulic protection. This ensures a perfect cutting quality regardless of working speed and crop. On the BIGMASTER 6 models the operation of the knife group configuration is easily done from the tractor cab via the terminal. On the BIGMASTER 5 models only two levers have to be moved. The operator can easily choose from the following knife group configurations: 0 – 11 – 12 – 23. The boltable rotor tines made out of Hardox® wear plate guarantee easy exchange (the BM 5712 features welded rotor tines). Together with the standard cassette system for easy knife changing, you not only invest in cutting quality but, above all, in driver comfort. Power Density: The Power Density system ensures optimum compression chamber filling with all types of forage, while also preserving the qualities of the forage itself. Whether working with the season's first harvest of lucerne, the large windrows typical of the first cutting in spring or straw, this system ensures the same, outstanding results, with tightly packed, evenly formed bales. The loader fork transfers the forage from the rotor to the compression chamber. When this pre-compression chamber is 100% full and the pressure reaches a predetermined value, the system automatically transfers the pre-compressed block directly to the compression chamber. Compression chamber: DEUTZ-FAHR's engineering excellence is evident in pistons and a compression chamber designed with the primary goal of producing extremely compact, tightly packed bales. The 3 meter long compression chamber ensures outstanding bale density. The piston is driven at a speed of 46 strokes/minute directly by the main transmission and is mounted on three or four 150 mm diameter roller bearings which run on specially treated slides. The roller bearings are lubricated by a centralised system and located outside the compression chamber for easy access for inspection and maintenance. The pressure may be preset directly from the cab of the tractor. In the event of overload, the machine reduces the pressure in the chamber to prevent the risk of damage. Once the overload has been cleared, the preset pressure is restored. All models are equipped with cam-actuated clutch protection systems for all the main feeder elements: namely, the pick-up, integral rotor and loader fork. High intake capacity: Intake capacity is one of the most important factors in profitability. That is why the SB series balers feature a high-performance crop intake system. The unique crop guard design, in combination with a high torque on the INTEGRAL ROTOR and on the feeder fork driveline, ensures a high intake capacity while offering extreme endurance. Smart design for more user convenience: The design of the BigMaster 6 models offers perfect accessibility to the inside of the machine during daily inspection and maintenance. For more safety, the knotter deck is equipped with solid stairs and a safety railing. The safety railing can be folded down easily to reduce the height of the machine during transport. Moreover, the driver can benefit from optimal comfort thanks to the heavy flywheel, the load sensing hydraulics and the torque regulation system. A perfect balance between capacity and density: The patented torque regulation system on all BigMaster 6 series 120 cm bale channel models ensures a perfect balance between capacity and density. The system consists of plunger rod load pins that measure the plunger force and an angle sensor that measures the crank angle. Throughout the complete plunger cycle the exact torque is calculated. The benefit of this sophisticated measuring method is that up to 5% higher bale density can be achieved when driving at a capacity of 25 t/h. This results in a higher transport and handling efficiency. Knotting: The TWIN STEP system on the BigMaster 5 series ensures trouble-free knotting. The knot is tied in two steps to create the ideal tension between the twine and knotters, for maximised bale density. The 4 or 6 knotters (depending on model) are lubricated by a centralised system, and may also be connected to an optional lubricator system. For additional peace of mind, to reduce the risk of machine damage and down-time, each knotter is protected by a shear bolt. The BigMaster D models are equipped with a double knotting system. With the electronic knotter control, the driver has accurate information concerning twine tension at all times and receives an alarm in case of risk. The knotting progress can be monitored directly from the tractor cab. Monitor and ISOBUS All models are fully ISOBUS compatible. This means the intuitive user interface can be displayed on all CCI terminals. The CCI 50 is a full ISOBUS terminal with a 5.6” colour screen. The CCI 1200 is our state of the art ISOBUS terminal. The 12.1” colour touchscreen has a programmable view.