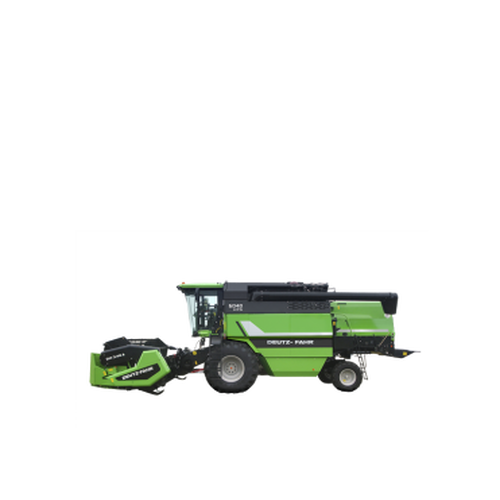
6040 Series
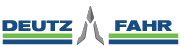
Max Power
250 Hp / 186.4 Kw
Displacement
6100 cm3
Grain Tank
6500 LT
SIMPLY PERFECT FOR EVERY CROP
The DEUTZ-FAHR 6040 Series evolves with the introduction of two new extraordinary models - the 6040 and 6040 HTS - which set a new benchmark for this segment of the combine harvester market. The culmination of many years of experience, these new models offer extraordinary levels of productivity and comfort. Unparalleled performance with types of crop with impressively low running costs, excellent results in terms of grain cleaning and integrity, and extremely simple maintenance.
The high performance cutter bars (measuring from 3.8 to 6.3 m in width) have a monolithic structure for superior weight distribution and stability, maximising durability and performance irrespective of cutting width. The large diameter feeder auger with broad spirals and helically distributed auger fingers ensures continuous feed and product transfer. Schumacher cutting system: The Tandem cutting system has an alternating surface for clean, quiet operation and minimised wear. A blade with individually bolted sections and an excursion of 105 mm also contributes to maximising performance and ensuring clean, precise cutting action in all conditions. The blade carrier tines are extremely sturdy and closely spaced to prevent the risk of foreign objects passing through and damaging the blades. The Schumacher system is driven by a planetary gear transmission: this extremely efficient solution allows very high cutting rates (1220 cuts/min) and maintains a perfectly straight blade alignment for superior mechanical efficiency, optimised power transmission and low maintenance costs. AutoControl: An electronic cutter bar control system, which keeps the cutter bar uniformly aligned in all terrain and crop conditions. This system also automatically damps cutter bar oscillations during transport to prevent the risk of damage to the mechanical components of the combine harvester. On the Topline version of the 6040 Series, the AutoControl function also corrects the transverse position of the cutter bar relative to the ground up to an inclination of 14%. This correction is implemented independently of combine harvester inclination, with specific sensors mounted on large metal feelers monitoring the status of the bar and transmitting the relative parameters to an electronic control unit, which adjusts the bar position accordingly. Pick-up reel: The pick-up reel consists of six sturdy toothed bars. Made from extremely resilient and flexible plastic, the teeth are individually replaceable and settable at an adjustable angle. The assembly slides along the arms on Teflon guides for quick, precise hydraulic adjustment of tooth inclination (even during use), and is also easily adjustable in position vertically or horizontally relative to the cab, to cater ideally for different harvesting conditions. Special kits: Two special kits for installation on the cutter bars (up to 6.3 metres in width) are available for harvesting sunflower seeds and rapeseed. This first kit consists of special extensions used together with a smooth cylinder (installed in front of the feeder auger) and a toothed roller (mounted under the cutter bar instead of the pick-up reel, which is removed) to harvest the crop efficiently and quickly. The kit for rapeseed differs from the sunflower seed kit as it also includes an extension for the table and a vertical cutter blade on the right hand side of the hydraulic transmission (or with a blade on the left hand side, as an option).
read moreThe feeder channel has rasp bars fastened to two chains; the carrier shafts are fitted with toothed guides to prevent slippage between chain links, to ensure continuous feed to the machine and prevent channel overload. The height of the front shaft is adjustable for threshing wheat or maize, while the intermediate shaft improves feed to the threshing drum and clears accumulated crop from the channel. Feeder channel inversion: Drive is via a two-groove V-belt (an optional three-groove V-belt is available for use with maize pickers) for efficient power transmission with minimised noise. The direction of the feeder channel and bar may be inverted electrically to prevent the risk of feed system overload. Cutting angle adjustment: In the standard configuration, the cutting angle is adjusted with mechanical tie-rods. As an option, an electrohydraulic cutting angle system is available, to optimise the position of the cutter bar for the direction of travel.
read moreA robust, reliable and highly productive threshing system that handles the crop delicately during grain separation. Threshing drum: The threshing drum has five straw walkers, measures 1.27 m in width and 600 mm in diameter, and is equipped with eight rasp bars (screw-mounted for quick and easy replacement) for a perfect threshing action. A high threshing frequency (120,000 beats per minute) means that even the most difficult to thresh cereals are processed with ease. Crop enters the threshing drum horizontally for uniform, blockage-free feed, while an access aperture above the feeder channel facilitates maintenance. Multi-segment concave: The multi-segment concave (4 mm wire diameter) is the ideal solution for quickly reconfiguring the combine harvester for different crops: this is done by simply removing the segments from the stone guard cavity of the concave and replacing them with specific components for the crop. The concave has fifteen rasp bars arranged with a pitch of 121 degrees, for superlative threshing and separation efficiency. The distance between the concave and the threshing drum (on both the inlet and outlet sides) is independently adjustable at the front and rear with easy to use levers, to ensure optimised operation in all crop conditions. And for crops that are particularly difficult to thresh, a set of manually fitted de-awning plates is also available. Thresher drum reduction gear: The threshing drum is equipped with an efficient variable speed transmission making is possible to set the ideal speed for each crop; the speed may be set and electronically maintained within a range from 420 to 1250 rpm, while an automatic variable speed transmission tensioner system protects belts and threshing drum against overloading. For particularly delicate crops, and additional reduction gear unit is also available to reduce the operating speed range of the threshing drum from the standard 420 - 1250 rpm to 210 - 625 rpm. Turbo-separator The HTS model is equipped with a turbo separator (590 mm diameter) with ten toothed rasp bars, which increases productivity by up to 20%. The system uses centrifugal force and an additional mesh (with a spacing of 40 mm) which adds 0.81 m² of surface area to the combine harvester, to ensure that every last grain is separated from the straw, even in the most challenging conditions - even with green straw or an infested crop. In this exclusive system, the turbo-separator may be set electrically into five different positions (for a drum excursion from 25 to 65 mm) and operate at two speeds: 775 rpm for crops with smaller seeds and 410 rpm for crops with heavier seeds. Straw walkers: The straw walkers have a very large surface area, are particularly long and have an extended excursion to separate the very last grain from the straw. The dedicated return pan is specifically shaped so that the crop already reaches the grain pan in stratified form; while the first step of the straw walkers is deeper, to slow the flow of crop exiting the threshing system and improve the efficiency of the first stage of separation. The straw walkers are mounted on special, hermetically sealed, maintenance-free bearings, which reduce noise and power loss and increase the lifespan of the shaft and of the straw walkers themselves. And for even greater separation efficiency, the straw walkers may be fitted with specific crests. Grain pan: The very long grain pan moves with a reciprocating motion to ensure perfect stratification of the chaff and straw. As these two components are lighter than the grain, they are blow away immediately upon contact with the air flow, increasing the efficiency of the sieves and the cleanliness of the finished product. The double pre-cleaning steps ensure superlative cleaning results without overloading the sieves. The grain pan is easily removable from the front of the combine harvester, significantly reducing the time necessary for cleaning and maintenance and simplifying the operations needed to reconfigure the machine for a different crop. Sieves and ventilation system: The sieves are mechanically operated and adjusted with levers (a system for electric sieve adjustment from the Commander Control is available as an option), are fitted with tall separator blades and are easily removable. Using dual sensors and a control bar extending along the entire width of the threshing tank, the sieve control system monitors the productivity of the combine harvester precisely. An external transmission system for the sieves and return pan prevents the risk of internal blockages in the cleaning system, for maximised efficiency. The high performance (400 mm diameter) turbine with 24 vanes aspirates air along the entire width of the combine harvester. The transverse air flow volume is controlled by deflectors which advance or retard air delivery to the sieve for uniform delivery over the entire length of the tank. DGR: The recovery system redistributes material that has already be treated over the grain pan: this solution prevents the risk of overloading the threshing system, causing the breakage or loss of straw walkers. Special friction inserts (with interchangeable types for different crops) exert an additional threshing action on the recovered grain, to separate any unseparated partial ears that have inadvertently reached the sieves. The recovery rate is monitored continuously and an alarm signal warns of overload conditions.
read moreThe turbine work in conjunction with the double step system to clean enormous quantities of crop, while the crop is fed back to the grain pan for maximum grain protection without overloading the threshing system.
read moreTank: The 6500 litre capacity grain tank is fed by a grain elevator which minimises the risk of grain disintegration and ensures that the tank itself is filled completely (while the level in the tank is observable via a window in the cab). Rapid emptying minimises time wastage, while powerful motors discharge the tank effectively while working, for no loss in productivity. An indicator light and audible warning signal in the cab activated by two sensors in the tank inform the driver that the tank is full, and that it is necessary to approach the thresher for discharging. Discharging: A discharging capacity of 75 l/min ensures that the tank is emptied rapidly and saves considerable time. The discharge speed my be adjusted with specific deflectors in the tank near the discharge auger. The high discharge outlet (4.3 m) means that the tank may be emptied even when moving, and allows product to be transferred easily even into large trailers. Measuring 5 metres in length and with a generous 110 degrees of mobility, the discharge pipe means that the combine harvester can work with a large range of cutting widths, and ensures that the operator has a clear view of the discharge outlet at all times. Tank discharge is possible in all discharge pipe positions, while the discharge outlet may be opened and closed from the Commander Control.
read moreStraw chopper: The integrated straw chopper is equipped with a rotor with 48 cutter blades arranged in four rows. This configuration produces an air flow which spreads material uniformly over the entire surface of the cutter bars. The distribution of material is adjusted with manually controlled deflectors (an electrical adjustment system is available as an option). The system may be set to chop straw or maize by simply changing two pulleys, without requiring additional reduction gears for threshing heavier crops. The position of the counter-blade is adjustable to obtain the degree of chopping required. Chaff spreader: Like the straw chopper, the chaff spreader is designed to distribute material over even the broadest cutter bars, for perfect mixing of the chopped material. The angle of the chaff spreader is adjustable to ensure ideal distribution with different crops and in different humidity conditions. The transfer pan (which transfers the product to be processed from the sieves) ensures uniform chaff distribution, while a conveyor with metal chutes directs the chaff to the four-blade rotors. The blades of the chaff spreader include specific deflectors which regulate air flow for superlative distribution results without very high power demands.
read moreThe engine of a combine harvester must be capable of powering additional or optional accessories such as straw choppers, maize heads, corn choppers etc., and must have a sufficient torque reserve to maintain maximum productivity even in the most challenging conditions, with no loss in threshing component speed. The modern 6 cylinder DEUTZ TCD 6.1 engines with common rail injection and four valves per cylinder combine outstanding power with extraordinary efficiency, for superior threshing performance with optimum fuel efficiency. Putting every ounce of power to work: Power is taken off from both ends of the crankshaft, making it possible to separate hydraulic and mechanical functions, and ensuring a direct transmission system with no power losses. This also means that fewer drive belts are used, and that the belts themselves are more accessible, reducing the running costs for the combine harvester. DCR SCR engine: What sets the DCR (Deutz Common Rail) system apart from other solutions is that it uses two injection pumps to feed the rail which are embedded in the cylinder block and lubricated with engine oil instead of diesel fuel. This solution is safer and more reliable than a conventional common rail system, as the lubrication of the pumps is not dependent on fuel flow. A pump delivery regulator system limits the quantity of fuel recirculated back to the tank, reducing pump load and fuel heating. SCR is an efficient exhaust after-treatment system which reduces nitrogen oxide emissions in the exhaust gas by selective catalytic reduction with AdBlue® additive. Three stage transmission: The hydrostatic three-stage transmission ensures the ideal ratio and speed for all harvesting conditions. The ideally spaced ratios ensure that there is always enough torque on tap to tackle even the most critical situation. The gears of the reduction unit and gearbox are lapped to reduce operating noise without compromising the durability and reliability of the transmission system. Hydraulics: The hydraulic system uses a triple pump layout to ensure adequate delivery in all conditions to cater for power demand. The solenoid valves are all situated on the left hand side of the machine and are easily reachable from the cab access platform.
read moreThe new “Commander Cab Evo” cab evolves the concept of the driver space to offer advanced technology and extraordinary levels of comfort. The air conditioning system maintains an ideal environment in the cab in all conditions, while the configuration of the console is specifically designed to place all the controls within easy reach of the driver without hampering visibility. The lighting system consists of eight work lights mounted on the cab with HB3 lamps which powerfully and clearly illuminate the work area without uncomfortable glare. An additional two work lights mounted on the straw walker cowl and a light illuminating the discharge pipe are also available. Commander control: All the instruments are organised rationally within the field of vision of the driver, while the controls are easily identifiable and arranged in relation to priority, for simple and immediate usage for total control over the machine. The functions of the cutter bar are controlled from the “Commander stick”. The CCM (Combine Control Management) module monitors the productivity parameters of the combine harvester (total and partial processed terrain area count, hourly production, losses, recovery level and cutter bar position) and lets the driver set the maximum values for losses and recovery in relation to grain size. The module also continuously monitors vital machine parameters such as total threshing hours and partial and total hours of engine operation.
read more